 |
“Si definisce
sovralimentazione l’operazione mediante la quale si precomprime l’intera
(od una parte della) carica fresca al di fuori del cilindro di lavoro, con
lo scopo di aumentare la massa di aria o miscela che un motore riesce ad
aspirare per ogni ciclo” (G. Ferrari, Motori a combustione interna). |
Composizione
Turbocompressore |
Il
turbocompressore
e' in sostanza una pompa accoppiata ad una turbina.
La pompa chiamata compressore (C.) che ha il compito di pompare il fluido
che nel nostro
caso e' l’aria, e' costituita da una girante e da una chiocciola di
raccolta del fluido.
La girante del C prende il moto da un alberino a sua volta azionato dalla
turbina (T)
La turbina (T.) e' di forma analoga al C .
L’alberino assialmente collegato al C e alla T fa si che questi due girino
ai medesimi g/m.
L’alberino inoltre ruota su dei cuscinetti volventi o a sfere all’interno
del carter :un corpo cilindrico che ne permette la lubrificazione ed il
raffreddamento.
Il compito della T. e' quello di trasformare l’energia termocinetica dei
gas di scarico in energia meccanica ,quello del cmpressore e' quello di
trasformare l’energia meccanica per ottenere aria compressa.
Le dimensione del C. e del T. come pure le loro proporzioni nonché i
profili delle giranti ne determinano il campo operativio. Queste macchine
operatrici sono di tipo asso-radiali.
Ossia accoppiano una sezione con un funzionamento assiale ad uno
radiale .
o modo
di parlarne |
Funzionamento |
In pratica, mediante un compressore, l’aria
viene immessa nei cilindri ad una pressione superiore a quella
atmosferica; ciò permette che una maggiore quantità di combustibile,
proporzionale all’ aumento di densità dell’aria precompressa, possa venir
bruciata all’interno del cilindro. Come risultato si ottiene un incremento
della potenza specifica ed un miglioramento del rapporto peso/potenza di
un dato motore.
Per comprendere meglio come la
sovralimentazione permetta di ottenere un aumento di potenza, si ricordi
come per un motore a quattro tempi (dove un ciclo completo viene compiuto
con due giri di manovella, corrispondenti a quattro corse del pistone)
S i
noti come a parità di cilindrata unitaria, due siano le strade
perseguibili per l’innalzamento della potenza: la prima è innalzare il
numero di giri, strada seguita dai motori aspirati, con la conseguente
ricerca di un alleggerimento delle masse in moto per ridurre l’inerzia; la
seconda è incrementare la pressione media effettiva ed è proprio
quella seguita dai motori sovralimentati.
La sovralimentazione permette di aumentare
la densità dell’aria (essendo la densità data dal rapporto massa/volume,
ad un aumento della massa si ha un aumento di
r)
ed il coefficiente di riempimento (all’apertura della valvola di
aspirazione, i gas residui della combustione vengono compressi dalla
carica fresca che quindi può occupare un volume maggiore con un
conseguente miglioramento di l): di
conseguenza sia la pressione media effettiva che la potenza utile
effettiva si accrescono.
La sovralimentazione presenta anche altri
vantaggi, quali il miglioramento del rendimento del motore (attraverso un
miglioramento del processo di combustione), cosa ancora più evidente nei
motori Diesel, dove si riesce a ridurre il ritardo di accensione, la
riduzione delle emissioni di particolato ed una combustione più graduale
che permette di avere un motore dal funzionamento più silenzioso.
Tra gli svantaggi si ha un aumento dei
carichi meccanici (determinato dalla maggiore pme) e termici.
Inoltre, per i motori ad accensione comandata, si verifica la detonazione
con il conseguente “battito in testa”: ciò perché una parte della miscela
si trova in condizione di autoaccendersi ancor prima di essere raggiunta
dal fronte di fiamma regolare.
Proprio per ridurre questi inconvenienti,
i motori sovralimentati presentano un rapporto di compressione inferiore a
quello degli aspirati. La riduzione del rapporto dì compressione determina
la riduzione dei picchi di pressione e delle temperature massime
sviluppate durante la combustione entro i limiti tollerati dal motore,
consentendo di aumentare pressioni e temperature medie effettive del
ciclo.
In tal modo si ottengono aumenti di potenza, coppia e carichi meccanici
medi, mentre si diminuiscono le punte di carico massimo sugli organi in
movimento.
Ora che qualche elemento teorico è stato
chiarito ci si può chiedere: come realizzare la sovralimentazione?
I due metodi più utilizzati sono il
compressore volumetrico ed il turbocompressore, mentre un terzo, il
Comprex, non viene utilizzato.
|
Compressore
Volumetrico |
Il compressore volumetrico è costituito da due lobi che
comprimono l’aria all’aspirazione; esso viene azionato direttamente
dal motore tramite una trasmissione a cinghia o a catena. Il vantaggio
principale di tale soluzione è che, essendo il compressore centrifugo,
azionato dal motore, la sovralimentazione è attiva già a basso numero di
giri: per questo motivo tale soluzione ha conosciuto una certa diffusione
nei rally. Lo svantaggio principale di tale soluzione è l’assorbimento di
potenza ai danni del motore.
|
Considerazioni |
Un'altra cosa da curare è lo scarico della turbina .
Dalla turbina in poi è’ bene che il flusso dei gas non sia ostacolato: :il
turbo funziona a salti di pressione (fra la
mandata e lo scarico)la presenza di una contropressione limiterà la
possibilità di sfruttare appieno l’energia dei gas.
In questi ultimi anni tutte le motorizzazioni sia diesel sia a benzina
usano un catalizzatore onde abbattere gli inquinanti inoltre le
più restrittive norme contro l’inquinamento acustico hanno imposto l’uso
di marmitte più restrittive tutto ciò comporta una
perdita di rendimento delle turbine.
Può in una certa misura compensare queste perdite l’uso di un diffusore
allo scarico della turbina ,questo infatti causerà una
aumento della velocità dei gas (non della massa) ed una diminuzione della
temperatura e quindi della pressione aumentando
al contempo il salto di pressione.
E’ pure utile (apprezzabile soprattutto ai bassi regimi) la realizzazione
di sistemi che limitino il reflusso dei gas di scarico dal collettore di
scarico ai cilindri :la presenza della turbina infatti crea una
contropressione allo scarico (delle onde di pressione) che crea appunto il
riflusso.
Questo è evitabile (o almeno limitabile) realizzando dei voluti salti fra
la testata (lato scarico) ed il collettore asportando da quest' ultimo una
quota di corona circolare e raccordandola dolcemente al proprio diametro
nominale.
Questo è applicabile un po’ ovunque : fra il collettore di scarico e la
turbina e all’uscita della turbina compatibilmente con l’eventuale
presenza del diffusore) e sul lato aspirazione.
La realizzazione degli anti-riflusso lato aspirazione è’ utile soprattutto
in caso di forte anticipo nell’apertura della valvola di aspirazione.
Questi accorgimenti migliorano la trattabilità del propulsore donandogli
una maggiore corposità e consistenza sin dai minimi regimi di rotazione,
con una più dolce entrata in coppia del
motore, anche se questo può provocare una diminuzione della massima
potenza erogabile stimabile in circa il 2%.
Occorre prestare attenzione alla carburazione del motore dopo
l’effettuazione di questi lavori infatti la fluidodinamica del motore
viene stravolta, e sopratutto nei motori ad iniezione è probabile che si
debba correggere la fase di iniezione per evitare che la miscela carburata
non fuoriesca dal cilindro attraverso le valvole di scarico creando
pericolosissimi smagrimenti.
Non so se i propulsori ad iniezione catalizzati (dotati di sistema
autoadattivo) siano in grado di compensare e correggere i parametri di
anticipo .
Pure l’anticipo di accensione necessita di essere corretto infatti i tempi
mappati nella centralina sono frutto delle condizioni operative del
motore.
Ma se la centralina è in grado di autoadattarsi alle nuove caratteristiche
operative del motore tempo qualche decina di chilometri effettuati nelle
più svariate condizioni operative del motore ( va escluso comunque il
range di potenza massima che puo' richiedere degli aggiustamenti di
carburazione ed accensione) esclusa la massima potenza con l’acceleratore
tutto aperto) ,il risultato sarà una erogazione che farà esclamare .
Anche la valvola a farfalla del motore potrebbe richiedere degli
aggiustamenti o addirittura la sostituzione con una più grande che
permetta causa minore perdite di carico un maggior afflusso d’aria al
motore.
E’ altresi’ importante il suo perfetto allineamento all’asse del condotto
e la totale assenza di oscillazioni.
E’ pero’ inutile intervenire in questo punto se i condotti di aspirazione
sono sottodimensionati, ma è di fondamentale importanza quando si sono
lavorati questi ultimi e se sono state maggiorate le valvole ,insomma in
tutti i casi in cui si è migliorata la fluidodinamica degli stessi.
Nel migliore dei casi una riprofilatura al top della valvola a farfalla
può dare incrementi di potenza anche del +5/10%.
Per riprofilatura al top si intende rendere aereodinamica la farfalla
assottigliandola ,riducendo il balestrino (ma senza indebolirlo), ed
eliminando le viti.
La riprofilatura della farfalla non richiede la rivisitazione dei
parametri della centralina ;al contrario la sua sostituzione con una dal
diametro maggiore permetterà a pari percentuale di apertura (intesa come
angolo) un maggiore afflusso d’aria e poiché la centralina gestisce
l’arricchimento in fase di progressione tramite un potenziometro che ne
misura l’apertura si ritroverà a gestire parametri a lei sconosciuti,
occorrerà quindi una riprogrammazione dei parametri.
|
L'
Intercooler |
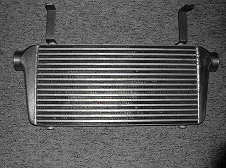
L’aria compressa in uscita dalla
girante del compressore ha una temperatura di più di 80°: per questo
motivo l’aria compressa, prima di essere immessa nel motore, viene
raffreddata per mezzo di uno scambiatore di calore aria/aria, altrimenti
detto intercooler. I vantaggi della post refrigerazione, in termini di potenza, sono
quantificabili
empiricamente: una diminuzione di 10
°C crea un aumento della massa volumica dell’aria pari al 3% a cui
corrisponde un incremento di potenza pari al 3,5%.
L'innalzamento della temperatura dell'aria
è determinato dall'introduzione di attriti da parte del compressore.
Questa quota di attriti (lavoro speso in più) comportano una
trasformazione isobara (a pressione costante), che va a sommarsi al lavoro
"adiabatico".
La presenza dell'intercooler nell' impianto di sovralimentazione comporta
anche questa volta una trasformazione isobara
r2/r1=T1/T2 dove r2 e' la densità dell'aria dopo la
trasformazione
r1 è la densità
dell'aria prima della trasformazione (1.29 alla temperatura di 0°C ad
1Atm)
T2 è la temperatura
dell'aria dopo la trasformazione (temperatura in °K)
T1 è la temperatura
dell'aria prima della trasformazione (temperatura in °K)
quindi
r2=T1/T2*r1
esempio:
se la temperatura in uscita dal compressore e' di 150°C e l'intercooler e'
capace di portarla a 50°C e si ipotizza una densità dell'aria in uscita
dal compressore di r150°=2.5
si ha:
r50°=(150+273)/(50+273)*2.5=3.27
la densità
dell'aria è aumentata considerevolmente e con essa la potenza:
r50°/r°150=1.308
densità +30.8%
potenza +30.8%
rispetto allo stesso motore privato dell'intercooler.
Purtroppo non è facile calcolare la densità dell'aria all'uscita del
compressore a meno che non si conoscano i rendimenti dello stesso.
Infatti calcolarla con le relazioni adiabatiche o limite portano a degli
errori grossolani (non si tiene conto degli attriti e quindi del lavoro
speso in più).
La soluzione è quella di misurare le temperature (con apposite sonde) di
ingresso ed in uscita dal compressore.
La differenza di temperatura fra la mandata e quella calcolata dalla
adiabarica assieme al volume trattato rende calcolabile il rendimento del
compressore.
Va da se che l' intercooler deve essere delle massime dimensioni possibili
e correttamente ventilato.
La misura della temperatura aria a valle dello stesso da delle corrette
indicazioni in merito al suo dimensionamento e dimensionamento e
posizionamento.
|
Detonazione e
Preaccensione |
I
fenomeni più pericolosi per un propulsore sono la detonazione e la
preaccensione nelle quali si può incorrere innalzando la pressione di
sovralimentazione.
Questi due eventi causati da una PME e da una temperatura in camera di
scoppio eccessivi possono portare alla distruzione del motore in pochi
secondi.
Premesso questo ogni sistema atto a scongiurarla e' benvenuto.
Le tecniche possibili sono tante: si va dalla decompressione del motore
all'uso di benzine speciali,passando anche per una drastica riduzione
degli anticipi di accensione.
Tutti i sistemi enunciati hanno dei pro e dei contro.
La decompressione del motore comporta un discreto esborso economico,come
pure l'uso di benzine speciali che possono arrivare anche a 20.000 lire al
litro.
La diminuzione dell'anticipo dal canto suo determina una diminuzione del
rendimento termodinamico,con conseguente diminuzione della potenza
peggioramento dell'erogazione ai bassi regimi e peggioramento dei consumi.
Un altro sistema e' quello di diminuire la temperature in camera di
scoppio e diminuire la richiesta ottanica del motore tramite l'iniezione
d'acqua nel motore che comporta un estrazione di calore notevole e che
verrà trattata più avanti.
Il problema potrebbe essere limitato usando candele dalla gradazione
termica più fredda ;dico potrebbe perché potrebbe essere causata anche da
punti caldi nella testata ad esempio bave di fusione che diventando
incandescenti provocano l’accensione della miscela prima dello scoccare
della scintilla , ma potrebbe pure essere causata da una eccessiva
velocità di compressione del pistone causata da bielle troppo corte.
|
L' Iniezione
d'Acqua |
La
soluzione peraltro impiegata con grande successo nella F1 nell'era dei
1500turbo e tuttora (senza poterne fare a meno) nel campo di rallye gruppo
A e WRC sta nell'iniezione d'acqua all'interno del motore.
il principio su cui si basa sta nell'estrazione di calore che l'acqua
comporta in camera di scoppio durante la sua evaporazione,e nella
diminuzione della richiesta ottanica del motore che ha in presenza di
umidità nell'aria.
Il
principio e’ semplice: la nebulizzazione dell’acqua nei condotti di
aspirazione del motore; quest’acqua nebulizzata entrando nella camera di
scoppio evaporerà assorbendo una certa quota di calore (proporzionale alla
sua quantità) che allontanerà i problemi sopra esposti.
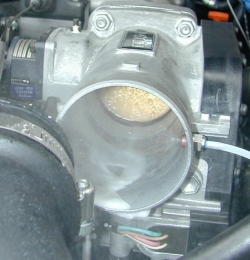
Un altro bonus dovuto a questa applicazione è l'effetto "pulivapor" che
l'acqua determina in camera di scoppio con la costante azione pulente su
pistoni,valvole e testata che questa esercita.
Per la sua realizzazione base e’ necessario munirsi di una pompa per
l’acqua capace di pressioni superiori di almeno 2bar a quella di
sovralimentazione ,di tubi in teflon ,di un ugello da applicare sul
condotto di alimentazione aria del motore ,di un filtro per l’acqua , di
un pressostato tarabile e di una tanica per l’acqua.
Le dimensioni dell’ugello vanno provate di volta in volta ma può essere
indicativo un diametro di 0.3-0.7 mm.
Questo sistema base permette l’erogazione dell’acqua al superamento del
limite impostato sul pressostato, ma la portata sarà costante (o un po’
decrescente al crescere della sovralimentazione).
Il passo successivo e’ quello di rendere l’erogazione dell’acqua
proporzionale alla pressione di sovralimentazione e meglio ancora anche al
numero di giri del motore magari collegando il tutto all’eventuale
debimetro.
Può essere parecchio utile dotare il serbatoio dell’acqua di un
galleggiante per segnalare la riserva, di una serie di diodi LED
che segnalino l’entrata in funzione dell’impianto.
L’aggiunta all’acqua di una percentuale variabile da0% ad un massimo del
50% di alcool metilico o etilico aumenterà la potenza
del motore allontanando al contempo possibili detonazioni.
Quanto questo impianto consenta di aumentare la potenza del motore non e’
facilmente stimabile, ma per dare un esempio una tipica vettura come la
Renault R5 GT TURBO in condizioni normali presenta detonazione con
pressioni della turbina intorno a 1.2 bar , con l’adozione della iniezione
d’acqua e’ possibile spingersi nei casi migliori anche a 1.8-2.0 bar , e
considerando che a queste pressioni la turbina originale (GARRETT T2) e’
parecchio fuori dal suo campo ottimale di funzionamento quindi con
temperature di mandata aria elevatissime e’ facile supporre che adottando
un turbocompressore maggiorato ed un adeguato intercooler si potrebbero
adottare pressioni ancora più elevate.
Uso il condizionale poiché con quelle pressioni sicuramente la guarnizione
di testa non resisterebbe per molti minuti!
N.B.
Nonostante su certa editoria specializzata venga proposto il montaggio
dell’iniettore a monte del compressore quale sistema pratico ed economico
, voglio mettere in guardia coloro che si facciano tentare.
Personalmente ho adottato questo sistema attirato dalla sua estrema
semplicità (si evitano le pompe a pressione e si utilizzano quelle dei
lavavetri), ma il suo uso ha decretato la distruzione della girante del
compressore, infatti seppur correttamente nebulizzata l’acqua incontrando
le palette della girante che ricordo possono raggiungere anche i 200.000
g/min con velocità periferiche elevatissime si comporta come un corpo
solido erodendo alla lunga il prezioso componente.
|
Blow By |
Durante il funzionamento del motore causa trafilamenti dei gas combusti in
camera di scoppio attraverso le fasce elastiche si
può avere nel
basamento un aumento (specie in presenza di forti sovralimentazione e di
motore consumato) un innalzamento
della pressione che
causa un accentuato passaggio di olio attraverso fasce e guidavalvole in
camera di scoppio aumentando la
possibilità che si
verifichi la detonazione.
Inoltre causa l’elevata pressione che può raggiungere diversi bar possono
sorgere problemi di lubrificazione anche per la turbina, infatti lo
scarico dell’olio di questa avviene generalmente per caduta in coppa ,ma
se vi e’ una elevata pressione questa può
creare problemi al suo
normale fluire.
E’ importante quindi migliorare lo sfiato del basamento o realizzarlo
ex-novo.
In genere la differenza fra un impianto mediocre ed uno ben realizzato è
quantificabile in 2-4CV.
In genere è sufficiente allungare il tubo di sfiato originale e portarlo
ad un serbatoio di raccolta di circa 1 Lt usando tubi del
maggior diametro
possibile ,Il serbatoio e’ bene che si trovi il più in alto possibile
compatibilmente con lo spazio disponibile .
Il serbatoio non deve essere ermetico bensì deve a sua volta scaricare i
vapori tramite un altro tubo (medesimi diametro) o
verso l’aspirazione del motore o in aria aperta (gli ecologisti
inorridiranno).
|
Consigli e
conclusioni |
Nel
preparare un motore turboalimentato e’ importante considerare la sua
destinazione d’uso ,bisogna distinguere infatti l’uso in competizione da
quello di un appassionato che comunque usa l’auto per spostarsi; in quest’ultimo
caso infatti e’ inutile avere un motore con un botto di cavalli ma
inguidabile nel traffico cittadino, e ancor peggio un motore che e’ poco
affidabile.
Per migliorare quest’ultima oltre a non esagerare con la pressione di
alimentazione cosa che per altro richiederebbe l’adeguamento di
guarnizione testa, prigionieri testa impianto di raffreddamento e di
lubrificazione adeguati, e’ utile munire la propria vettura di una serie
di strumenti di monitoraggio del motore cosa che farebbe rassomigliare
l’abitacolo alla cabina di guida di un aereo a reazione.
Benvengano quindi :un termometro per il controllo dei gas di scarico che
non dovrebbero mai superare gli 850°C,monitorare la temperatura dell’olio
motore (quando l’auto non ne sia già provvista),temperatura aria
sovralimentazione, lettura della sonda lambda per il controllo della
carburazione (la tensione dovrebbe aggirarsi intorno gli 0.8-0.9 V alla
massima potenza).
Per quanto possa sembrare strano pure i cavi candela hanno la propria
importanza infatti causa dispersioni possono verificarsi delle mancate
accensioni e con certe pressioni la quantità di benzina e’ tale da lavare
i cilindri e provocarne il grippaggi ,senza contare poi le esplosioni che
si verificherebbero a livello di collettori o catalizzatre.
Quindi sempre al massimo della loro efficienza meglio se di quelli
siliconici.
Nonostante si sia già affrontato il discorso sulle candele ritengo
opportuno ripetere l’importanza della corretta scelta del loro grado
termico.
Inoltre esistono varie configurazioni di elettrodi proposti dalle varie
case produttrici anche qui’ si possono ottenere dei miglioramenti
effettuando opportune scelte.
Ancora sulle candele e sugli impianti di accensione si puo' dire che in
caso di livelli di sovralimentazioni particolarmente elevati possono
sorgere problemi di accensione (misfire).
La specialità dei dragster affronta giornalmente queste problematiche che
vengono aggirate con impianti di accensione capaci di sviluppare tensioni
doppie e triple rispetto a quelli della grande serie e con l'uso di
candele speciali che fanno uso di metalli nobili come il platino ,
l'iridio e palladio.
In conclusione si può
affermare che la sovralimentazione è diventata ormai parte integrante dei
motori a ciclo Diesel, ma che probabilmente si assisterà ad un suo
utilizzo massiccio anche nei motori a ciclo Otto, ai fini di migliorarne
il rendimento e ridurne le emissioni inquinanti.
|
Thank's to Fabrio e cuorialfisti.com |